How can AR improve your Overall Equipment Effectiveness (OEE) and why is it Important For Your Business? (Atheer)
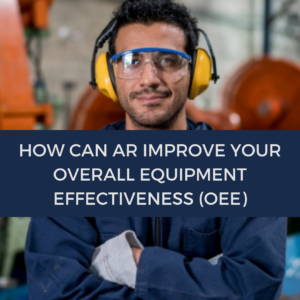
Manufacturers refer to Overall Equipment Effectiveness (OEE) as the gold standard of productivity for a reason. It’s putting it mildly to say your equipment’s availability to perform at the highest level and output high-quality products are essential to your company’s success. Tracking your equipment’s efficiency is the first step to improving it. Most manufacturers operate at between 60 and 65% OEE. World-class OEE is 85% or better.
What is OEE?
As was mentioned above OEE refers to Overall Equipment Effectiveness. This productivity score was invented by Seiichi Nakajima, the pioneer of the Total Productive Maintenance system.
Nakajima’s lifelong goal was to try to establish a near-perfect production method. He emphasized the necessity of proactive and preventive maintenance to maximize the productivity and longevity of equipment. The OEE score is derived from three factors: Availability, Performance, and Quality.
“Simply put –OEE identifies the percentage of manufacturing time that is truly productive. An OEE score of 100% means you are manufacturing only Good Parts, as fast as possible, with no Stop Time. In the language of OEE that means 100% Quality (only Good Parts), 100% Performance (as fast as possible), and 100% Availability (no Stop Time).” – OEE.com
OEE helps companies identify losses, benchmark success, find sources of waste in their processes and eliminate them. This has become even more important in an extremely competitive landscape. Even a 1% lift in OEE can offer companies huge benefits.
It should be noted that the concept of Overall Equipment Effectiveness was created during a different era of manufacturing. Nakajima’s world view considered unreliable machines as the biggest sources of failure on the line, because in the 1980s machines were much more likely to fail or be unreliable. In the last few decades machines have become 20 times more reliable.
The source of errors in factories is now more likely to come from the systems that govern the human element of the equation. As production lines put out more products, work with machines that are more complex, it becomes impossible to hold everything you have to know in your head or even in a three-ring binder.
Nakajima imagined humans as perfect cogs to keep the factory’s machines up and running. He didn’t think that the human element could be optimized and this is because he came up with his calculation prior to the invention of digital Front Line Worker tools.
3 Factors for Determining OEE: Availability, Performance and Quality
OEE Availability
Availability score takes into consideration planned and unplanned stops in production. A 100% availability score means the machines were running during all of the planned production time. What hampers Availability score is the length of planned stops and the frequency and longevity of unplanned downtime.
Machine monitoring and the accompanying service tasks performed by your workforce are what protect against these disruptions. Paper-based monitoring, unfortunately, siloes valuable data and makes it difficult for management to have the necessary visibility to order preventive maintenance and reduce unplanned downtime.
OEE Performance
Performance score takes into account slow cycles and small stops in production. A performance score of 100% means the process is running at the fastest possible speed. What hampers performance are inefficient idling and minor stops and reduced speed of production.
In most manufacturing shop floors, machine idle time can be as much as 40% – reducing the ROI by 30%. Paper-based reporting for machine monitoring and related service tasks means much of these losses go unaccounted for because the time in between tasks simply aren’t being tracked. This denies management real-time visibility on what’s happening on the manufacturing floor.
OEE Quality
The quality score takes into account defects and parts that need to be reworked. A quality score of 100% means that only good parts were produced. This is in general the hardest aspect of OEE to improve as most manufacturing companies have by necessity created production lines that create little defective parts. After all, people aren’t going to buy products that don’t work!
Why Is It Important to Improve OEE?
You might be thinking OEE sounds cool and maybe a little nerdy. But what does my company get from tracking it?
Return on investment
Manufacturing companies spend massive amounts of money on getting state-of-the-art equipment and need to maximize the return on their investment. By improving OEE a company can increase productivity and get more longevity out of its equipment.
Staying ahead of the competition
If your equipment breaks down and you can’t meet your customer’s needs, they’ll go to your competitors. With supply chains increasingly strained it’s never been more important to get the most out of what you already have.
Iterate and improve
Once you’ve begun to accurately measure your company’s OEE you can begin to implement process iterations and assess whether the new processes are working through data analysis. Effectively measuring OEE allows companies to push forward innovation projects because they can directly show the financial benefit to upper management.
Discover your process efficiency
As a rule of thumb, a company’s production efficiency is actually much lower than assumed. By properly tracking production, companies can begin to unearth big gains by finding small inefficiencies and eliminating waste.
Reduce machinery repair costs
By tracking OEE you can optimize your preventive maintenance practices. It’s much less expensive to proactively repair equipment than it is to wait until systems fail.
Increase process quality
With greater process transparency it is easier to discover where defects can be found in your production line.
Read Atheer’s AREA member profile
Visit Atheer’s website