Atheer Air’s new release increases capabilities and productivity for enterprises
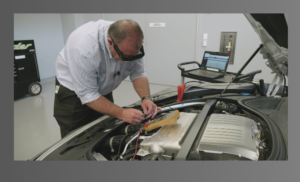
The new release is designed to further empower enterprises with richer reporting and analytics, enhancements to the “See What I See” video call experience and ease of use updates that allow mobile device users to be more productive, more quickly.
The new release also expands the range of supported devices to include the recently-released Vuzix M300XL smart glasses and the Samsung Galaxy S6, S8 and Google Pixel 2XL mobile phones.
Reporting and Analytics Dashboard
A well-designed reporting and analytics dashboard is a vital information management asset for enterprises. In this release, Atheer provides a new dashboard to provide at-a-glance insight into how effectively business processes are being completed and the overall level of workforce engagement with the AR platform. Key metrics tracked by the dashboard include statistics on platform’s top users, number of calls and taskflows completed (a taskflow is a set of work instructions) – as well as the number of messages sent and the average duration of calls.
Screen Sharing for Web Users
In the course of their work, an enterprise employee in the field will often use their mobile device (smartglasses, a smartphone or a tablet) to make a video call to a remote expert or a colleague using Atheer. Typically, the scenario will involve the field employee sharing what they see and then having the remote expert annotate what the field employee sees – or send digital guidance including work instructions or annotated digital phones – to help them carry out their job.
Now, those remote experts can actually share their screens using the Atheer web console and enrich the ways in which they can help field employees. Screen sharing allows remote experts to move from being able to share specific digital assets with field employees to being able to share anything on their screen.
This new feature gives Atheer remote experts the ability to share their web-based screens during video calls with one or more web and device users. Those users can also now use annotations while sharing their screen, allowing more precise and effective collaboration.
Get More Productive, More Quickly
When using AR-enabled mobile devices, particularly smartglasses, starting applications can be tedious and time-consuming. To help enable users to be more productive, more quickly, Atheer introduces a “Kiosk Launcher” option in this release, which allows smartglasses to launch the Atheer app by default without having to navigate to it or go through any other intermediate start-up processes.
This new capability also makes access to the Atheer app more efficient for multiple users on the same device, because it allows the device to boot directly to – and stay in – the Atheer app without any user login.
Greater Device Choice and OS-specific Enhancements
The new Atheer release adds to the list of supported devices. The Atheer platform is now optimized for use on Vuzix M300XL smart glasses and additional mobile devices including the Samsung Galaxy S6, S8 and the Google Pixel 2XL.
In addition, this release includes many other enhancements including the arrival of contextualization on the Atheer iOS app – which allows users to retrieve specific content by scanning QR codes. As well, the new Android version of Atheer now includes the ability to force “over-the-air” updates to ensure users always access the most optimized version of the app based on their organization’s update settings.