Enterprise Augmented Reality Solutions – Build or Buy?
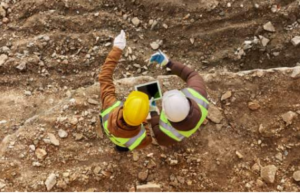
Short of time? Listen to the accompanying podcast (~8 minutes) available here.
This is a question with no simple answers. As enterprises contemplate deploying AR solutions, one of the first questions to confront them is a fundamental one: should we build or buy? This AREA editorial explores the factors that may help organizations answer this critical question.
The build-or-buy decision essentially boils down to determining the relative priorities of cost, control, solution availability and time to market. In traditional solution deployments, the advantages and disadvantages of each approach can be summarised as in the table below.
Consideration for Enterprise Augmented Reality
When it comes to enterprise AR deployment, the build-or-buy deliberations need to take in additional considerations. These may include some or all of the following:
- Implementations on novel or unfamiliar hardware
- Development of advanced computer vision capabilities
- Application development based upon AR toolkits
- Data processing, protection and optimisation (e.g. for 3D models)
- Integration into enterprise business systems
- Development of custom content for new methods of deployment and user interaction
- Customisation of the base solution to meet specific needs
A previous AREA editorial explored how AR should be considered within the scope of a technology strategy. For the purposes of this editorial, we shall omit custom hardware development from the discussion, but rather, focus on the software build-or-buy decision. There may also be wider implications if significant customisations are needed or content must be created by internal or external personnel.
Here’s a typical set of steps leading to the decision-making phase:
- Identify business use case, perform investment analysis and secure budget.
- Define weighted requirements for the solution to the identified business problems or opportunities.
- Identify potential vendors and their commercial solutions.
- Perform a gap analysis between commercial offerings and solution requirements.
- Identify whether gaps can be closed with customisation or custom development.
- Perform cost analysis of internal/external development versus commercial solution.
- Evaluate options and make strategy decision.
Target use cases are an important factor
It’s important to understand that enterprise AR-based solution needs may vary significantly according to the target use case. For example, the table below provides a view on how aspects of the solution needs vary across four example applications of AR for business use cases:
Such factors may play an important influence in the build-or-buy process. Take the AR-enhanced product demonstrator (sales) use case above, for example. The low levels of integration with business systems and data that this solution requires, coupled with other factors such as time criticality and reduced longevity needs, may make it appropriate to subcontract all software development and content creation to a third party.
If your use case is unusual, then you may need to consider purchasing an AR platform that allows custom development (whether via drag’n’drop authoring, coding or other mechanisms).
Example checklists
Typical questions to consider when making the build-or-buy decision are as follows:
- Have you identified the business applications (or problems to solved)?
- Have you developed the requirements needed to address the business problem?
- Are there commercial offerings claiming to provide a solution for your use cases?
- Are you confident that the solution meets your functional requirements?
- Would more than one commercial product be needed to provide the solution?
- Are you confident of the solution provider’s financial viability?
- Are there gaps between the commercial solution and your requirements? Are these gaps important and/or able to be closed? Are there other edge cases to be considered?
- Do you have the required skills in-house? Alternatively, are there vendors who can supply the skills within budget?
- What toolkits are available that can help provide the underpinnings of a custom solution?
- Is complete control and ownership of the solution important to your business (for reasons of market differentiation, security or others)?
The following table offer some additional important considerations more specific to an AR-based solution:
Choose wisely – and consult experts
This editorial has explored a number of considerations that are important when seeking to adopt AR in an enterprise setting. Companies may be tempted to develop prototype applications when first investigating AR, perhaps using one or more of the commercially available toolkits. However, there are clearly a number of important aspects to consider in reaching a build-or-buy decision.
It is unlikely that an industrial company will develop an in-house AR application from the ground up, as this requires significant expertise in numerous areas, including computer vision, 3D computer graphics, mobile device management, etc. If your use case is truly unique and there are no commercial products that support the use case, then your only option may be to develop the solution this way.
Far more likely, however, is the decision to purchase a commercial-off-the-shelf solution. As we’ve discussed, and depending upon your target use case, there may be significant requirements on systems integration, data processing, content creation and other forms of customisation required prior to considering a deployable solution.
As discussed above, the decision is often driven by requirements of cost, control and timing. If cost and timing are a higher priority, then a commercial offering is likely the more appropriate solution. If control is most important, then it is perhaps better to pursue internal development or, more likely, contracting the work to a third party.
Ultimately, the decision is yours. However, prior to making that decision, we recommend that you look at the offerings of the AREA solution provider members who will be happy to discuss and hopefully meet your requirements.